SMT加工焊膏使用流程及常见缺点避免或解决方法
时间: 2015-11-12 信息来源: 本站
SMT加工焊膏使用流程及常见缺点避免或解决方法
一.贴片加工中为保证表面贴装产品质量,必须对生产各个环节中的关键因素进行分析研究, 制定出有效的控制方法。
作为关键工序的焊膏印刷更是重中之重,只有制定出合适的参数,并掌握它们之间的规律,才能得到优质的焊膏印
刷质量。
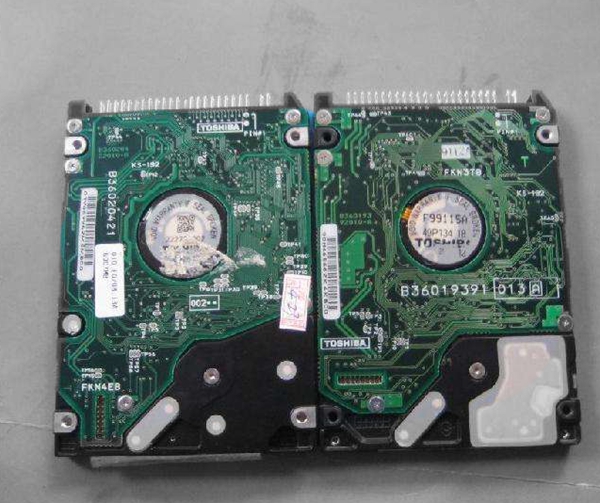
贴片加工锡膏使用时的注意事项:
1、生产前操作者使用专用设备搅拌焊膏使其均匀,最好定时用黏度测试仪或定性对焊膏黏度进行抽测。
2、生产过程中,对焊膏印刷质量进行 100% 检验,主要内容为焊膏图形是否完整、厚度是否均匀、是否
有焊膏拉尖现象。
3、在印刷实验或印刷失败后,印制板上的焊膏要求用超声波清洗设备进行彻底清洗并
晾干, 以防止再次使用时由于板上残留焊膏引起的回流焊后出现焊球。
4、严格在有效期内使用焊膏,平日焊膏保存在冰箱中,使用前要求置于室温6 h以上,
之后方可开盖使用,用后的焊膏单独存放,再用时要确定品质是否合格。
5、当日当班印刷首块印刷板或设备调整后,要利用焊膏厚度测试仪对焊膏印刷厚度进
行测定,测试点选在印制板测试面的上下、左右及中间等 5 点,记录数值, 要求焊膏厚度范围在模板厚度
的 -10% ~ +15%。
6、当班工作完成后按工艺要求清洗模板。
二.SMT生产中常见缺点避免或解决方法总结入选
1、拉尖,一般是打印后焊盘上的焊膏会呈小山状。产生原因:可能是刮刀空隙或焊膏黏度太大造成。
避免或解决办法:SMT贴片加工适当调小刮刀空隙或挑选适宜黏度的焊膏。
2、焊膏太薄。
产生原因有:1、模板太薄;2、刮刀压力太大;3、焊膏流动性差。
避免或解决办法:挑选适宜厚度的模板;挑选颗粒度和黏度适宜的焊膏;下降刮刀压力。
3、打印后,焊盘上焊膏厚度不一。
产生原因:1、焊膏拌和不均匀,使得粒度不共同。2、模板与印制板不平行;
避免或解决办法:在打印前充分拌和焊膏;调整模板与印制板的相对方位。
4、厚度不相同,边际和外表有毛刺。
产生原因:可能是焊膏黏度偏低,模板开孔孔壁粗糙。
避免或解决办法:挑选黏度略高的焊膏;打印前查看模板开孔的蚀刻质量。
5、陷落。打印后,焊膏往焊盘两头陷落。
产生原因:1、刮刀压力太大;2、印制板定位不牢;3、焊膏黏度或金属含量太低。
避免或解决办法:调整压力;从头固定印制板;挑选适宜黏度的焊膏。
6、打印不完全,是指焊盘上有些地方没印上焊膏。
产生原因有:1、开孔堵塞或有些焊膏黏在模板底部;2、焊膏黏度太小;3、焊膏中有较大尺度的金属粉末颗粒;
7、刮刀磨损。
避免或解决办法:清洗开孔和模板底部; 选择黏度合适的焊膏,并使焊膏印刷能有效地覆盖整个印刷区域;
选择金属粉末颗粒尺寸与开孔尺寸相对应的焊膏; 检查更换刮刀。